Plasmaunterstützte chemische Gasphasenabscheidung
Beschichtungen in der Halbleiterindustrie und Photovoltaik
Die plasmaunterstützte chemische Gasphasenabscheidung, oft einfach als PECVD bezeichnet, stellt ein zyklisches CVD-Verfahren dar. Dieses zeichnet sich durch seine besondere Fähigkeit aus, oberflächenkonforme Schichten mit hoher Präzision in ihrer Dicke abzuscheiden.
- Ermöglicht Beschichtungen bei niedriger Temperatur
- Geeignet für temperatursensible Substrate wie Kunststoff
- Komplexe Bauteilbeschichtung möglich
Erfahren Sie mehr über diese zuverlässige und präzise Technik in der Dünnschichttechnologie.

So funktioniert's
Was steckt hinter der plasmaunterstützten chemischen Gasphasenabscheidung?
Bei der plasmaunterstützten chemischen Gasphasenabscheidung, kurz PECVD, wird Plasma verwendet, um eine chemische Reaktion zu unterstützen. Der Vorteil dieser Methode ist, dass niedrigere Temperaturen zwischen 200 °C und 500 °C genutzt werden können. Dies ist besonders schonend für das Substrat, auf welches die Schicht aufgebracht wird.
In der Direkt-Plasma-Methode kann das Plasma direkt neben dem Substrat gezündet werden. Dieses Verfahren birgt jedoch bei empfindlichen Substratmaterialien wie Halbleiterwafern die Gefahr, diese zu beschädigen. Deshalb wird häufig auch die Remote-Plasma-Methode verwendet, bei der das Plasma räumlich vom Trägermaterial getrennt wird – eine Barriere schützt das Substrat vor Schäden und ermöglicht außerdem die selektive Anregung von einzelnen Bestandteilen des Prozessgasgemisches. Bei diesem Vorgehen ist es jedoch wichtig, sehr genau darauf zu achten, dass die chemische Reaktion erst dann erfolgt, wenn die aktivierten Teilchen die Oberfläche des Substrates erreichen.
Diese „Niedertemperatur-CVD“-Verfahren werden häufig eingesetzt, wenn das Substrat, z. B. Kunststofffolie, keinen hohen Temperatureintrag verträgt. Auch die Halbleiterindustrie setzt auf diese Methode, um eventuelle Strukturveränderungen im Halbleiter zu vermeiden. Zudem kann mit der PECVD-Technologie eine große Bandbreite an Materialien, wie amorphes Silizium, Siliziumnitrid oder Siliziumoxid für die Mikroelektronik abgeschieden werden. Die PECVD-Anlagen der FHR sind kundenspezifisch ausgelegt und speziell an die jeweiligen Prozessanforderungen angepasst. PECVD-Kompartimente werden zudem häufig eingesetzt, um die technologische Bandbreite von Sputter-Anlagen zu erweitern. Die FHR überzeugt in jedem Fall durch wettbewerbsfähige Preise und exzellente Anlagenqualität.
Die plasmaunterstützte chemische Gasphasenabscheidung (PECVD) bietet verschiedene Vorteile:
- Oberflächenkonformität: Die PECVD ermöglicht die Abscheidung von Schichten, die sich eng an die Topologie des Substrats anpassen, was besonders wichtig für strukturierte oder unebene Oberflächen ist.
- Niedrige Verarbeitungstemperaturen: Durch den Einsatz von Plasma kann die PECVD bei niedrigeren Temperaturen als bei traditionellen CVD-Verfahren durchgeführt werden, was besonders vorteilhaft für temperaturempfindliche Substrate ist.
- Vielseitigkeit: Die PECVD kann für eine Vielzahl von Materialien verwendet werden, einschließlich Dielektrika, Halbleiter und Metalle, was sie zu einem flexiblen Werkzeug für verschiedene Anwendungen macht.
- Hohe Qualität der Schichten: Die PECVD erzeugt oft dichte, homogene und pinholefreie Schichten, die für viele Anwendungen in der Halbleiterindustrie und Optik entscheidend sind.
- Feine Kontrolle über Schichteigenschaften: Mittels PECVD können die Eigenschaften der abgeschiedenen Schichten, wie Dicke, Brechungsindex und Stress, durch Änderung der Prozessparameter genau gesteuert werden.
- Umweltfreundlichkeit: Viele PECVD-Prozesse verwenden weniger toxische und gefährliche Chemikalien als andere Abscheidungsverfahren, was zu einem geringeren ökologischen Fußabdruck führt.
Vakuumbeschichtungsanlagen
Erfahren Sie, wie unsere Vakuumbeschichtungsanlagen in verschiedenen Branchen Hochleistungsbeschichtungen ermöglichen. Unsere Experten zeigen Ihnen, wie Sie unsere Technologien für Ihre Projekte optimal nutzen können.
So funktioniert´s
Das steckt hinter der Chemischen Gasphasenabscheidung
Die Methode „Chemical Vapor Deposition“ (CVD) ist eine bekannte Methode zur Aufbringung dünner Schichten auf Materialien. Dabei wird ein Material erhitzt und durch eine chemische Reaktion entsteht eine dünne Schicht aus der Gasphase auf diesem Material. Die FHR bietet spezielle Lösungen für diese Art der Beschichtung an, besonders für Drähte und Fasern, z.B. aus Kohlenstoff oder Siliziumkarbid.
CVD-Beschichtungen benötigen hohe Temperaturen von mindestens 500 °C und eine hohe Energiezufuhr. Ein Vakuum in der Prozesskammer vereinfacht den Prozess, indem es den Siedepunkt für den Übergang von Precursor-Substanzen in die Gasphase reduziert und unerwünschte chemische Reaktionen verhindert.
Ein Vorteil der CVD-Methode im Vergleich zum Beispiel zum PVD-Verfahren ist, dass sie auch komplexe und dreidimensionale Oberflächen gleichmäßig beschichten kann. Dadurch ist es möglich, auch sehr feine Strukturen auf Halbleiterscheiben, sogenannten Wafern, zu erzeugen.
Für die CVD-Beschichtung werden spezielle Ausgangsstoffe benötigt, welche alle notwendigen Bestandteile für die gewünschte Schicht enthalten. Zum Beispiel werden für eine Siliziumnitrid-Schicht als Ausgangsstoffe Ammoniak und Dichlorsilan eingesetzt. Für Wärmeschutzschichten auf Glas aus Zinnoxid werden Zinnchlorid oder zinn-organische Verbindungen sowie Sauerstoff oder Wasserdampf genutzt. Solche Zinnoxid-Schichten schützen zum Beispiel auch Behältergläser in Abfüllanlagen vor Beschädigungen durch Stöße und andere mechanische Einwirkungen.
Da der Zustand der Substratoberfläche Einfluss auf das Schichtwachstum hat, ist es bei entsprechender Auslegung des Prozesses möglich, Metalle gezielt in bestimmten Abschnitten der Oberfläche aufwachsen zu lassen – beispielsweise nur in elektrisch leitfähigen Bereichen, nicht aber in isolierenden. Diese Möglichkeiten zur selektiven Beschichtung machen CVD und PECVD besonders interessant für die Mikroelektronik.
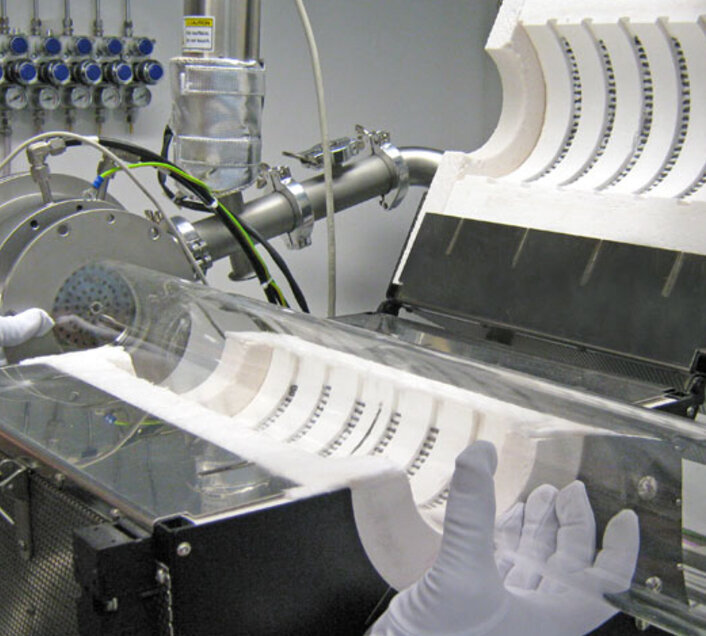
Weitere Technologien und Beschichtungsverfahren
Der richtige Partner an Ihrer Seite
Gemeinsam die Zukunft gestalten – mit zuverlässigen und hochwertigen Beschichtungslösungen der FHR:
- Branchenführende Qualität: Unsere Vakuumbeschichtungsanlagen sind auf höchste Präzision und Langlebigkeit ausgelegt.
- Maßgeschneiderte Lösungen: Wir bieten individuelle Lösungen für Ihr Beschichtungsprojekt, die Ihren speziellen Anforderungen gerecht werden.
- Innovative Methoden und Technologien: Mit unserer langjährigen Erfahrung und Expertise bei der Vakuumbeschichtung setzen wir neue Standards.
- Engagierter Kundenservice: Unser erfahrenes Team steht Ihnen jederzeit zur Verfügung, um Ihre Fragen zu beantworten und Sie bei Ihren Projekten zu unterstützen.
Entdecken Sie die vielfältigen Möglichkeiten unserer Vakuumbeschichtungstechnik und vertrauen Sie auf die FHR als Ihren zuverlässigen Partner für herausragende Beschichtungslösungen. Kontaktieren Sie uns, um mehr zu erfahren und gemeinsam Ihre Projekte zu realisieren.
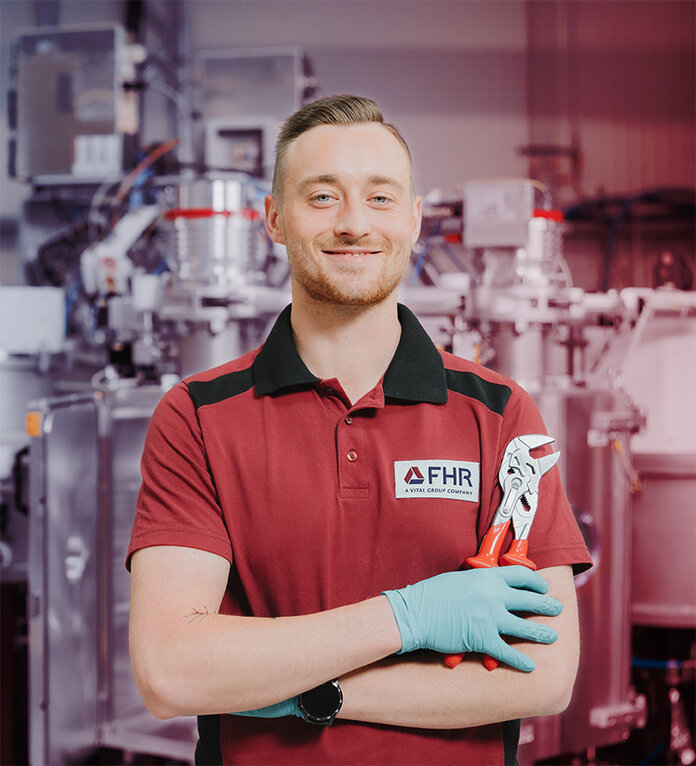
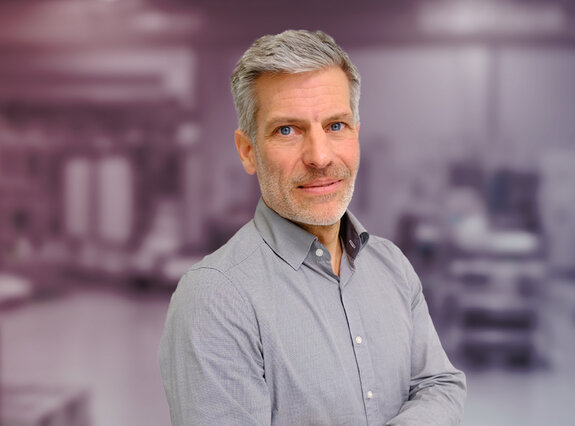
Ihr Ansprechpartner
Sie haben Fragen?
Sie wollen mehr über Dünnschichttechnologie erfahren oder sich ganz allgemein zu unseren Vakuumbeschichtungsanlagen und unserem Beschichtungsservice beraten lassen? Dann melden Sie sich bei uns – unser Expertenteam beantwortet gerne all Ihre Fragen.