Dünnschichtsensoren Cluster
Flexibles Beschichtungssystem zur Herstellung diverser Sensoren
APPLIKATION
Selbstfahrende Autos werden Realität, Smartphones verwandeln Laien in Messgeräteexperten und Hobby-Tüftler erschaffen mit Mini-Computern automatisierte Systeme für Zimmerpflanzen. Heutzutage ist komplexe Automatisierung kostengünstig und allgegenwärtig. Dafür unverzichtbar: eine Vielzahl an Sensoren. Sie erfassen Daten wie Temperatur, Abstand, Druck, Kraft, Luftfeuchte, pH-Wert, Gas-Konzentration und mehr, um aus theoretischen Simulationen praktische Alltagshelfer zu machen.
ANFORDERUNGEN AN DIE ANLAGE
Mit der Anlage sollen Sensoren produziert werden, d. h. Leiterbahnen, Kondensatoren, Widerstände, piezoresistive Schichten usw. werden auf 200 mm Wafern abgeschieden. Diese dünnen Schichten aus Metallen, Oxiden oder Nitriden müssen über den ganzen Wafer hinweg mit einer Schichtdickenabweichung von weniger als +/- 3 % aufgebracht werden und müssen gut auf dem Untergrund sowie aufeinander haften. Die Anlage muss zum SEMI-Standard kompatibel sein, damit vor- und nachgelagerte Prozesse aus der Halbleiterindustrie (z. B. zur Strukturierung) eingesetzt werden können. Überdies muss die Anlage natürlich vollautomatisiert Rezepte für verschiedene Sensoren fahren können und ohne äußeres Zutun ein ganzes Los von Substraten am Stück beschichten. Schließlich muss die Anlage flexibel und in der Zukunft erweiterbar sein, um auch kleine Lose spezieller Sensoren darauf herstellen oder neue Technologien zur Sensorherstellung (z. B. Atomlagenabscheidung) nachträglich integrieren zu können.
LÖSUNG DER ANFORDERUNGEN
Die FHR.Star.300 ist eine zum SEMI-Standard kompatible Vakuumanlage. Die zentrale Kammer ist mit einem Roboter ausgestattet, der die Wafer zwischen den ringsherum angeordneten Kammern transportiert. Die Wafer in der Eingangsschleuse werden je nach Rezept nacheinander in den vier Prozesskammern vorbehandelt bzw. per Sputtern mit verschiedensten Schichten versehen (DC-Sputtern, gepulstes DC-Sputtern, reaktives DC-Sputtern), bevor sie der Roboter in der Ausgangsschleuse ablegt. Die abgeschiedenen Materialien können durch Wahl der Targets geändert werden. Zwei freie Ports ermöglichen die spätere Nachrüstung weiterer Prozesskammern. Wie bei allen FHR-Anlagen wird auch hier per Rezept alles automatisiert gesteuert und alle Daten zur späteren Nachvollziehbarkeit aufgezeichnet.
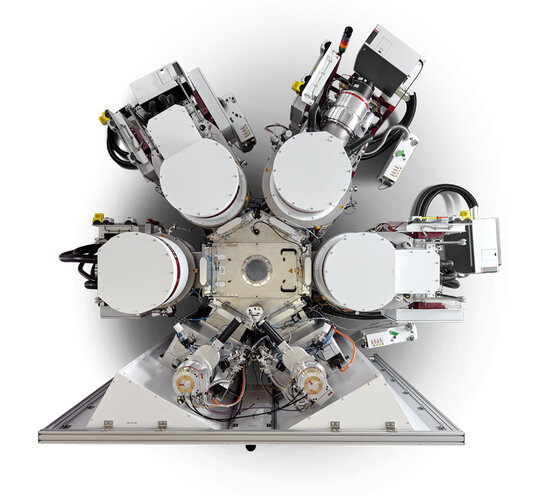
DIE BESONDERHEITEN DER FHR.Star.300
- Vielfältige Sputter- und Ätzverfahren in einer Anlage
- Wafergrößen bis 200 mm
- Automatisierte Beschichtung mit voller Kontrolle über alle Prozessparameter
- Komfortabler Wechsel der 300 mm großen Targets
- SEMI-Standard kompatibel
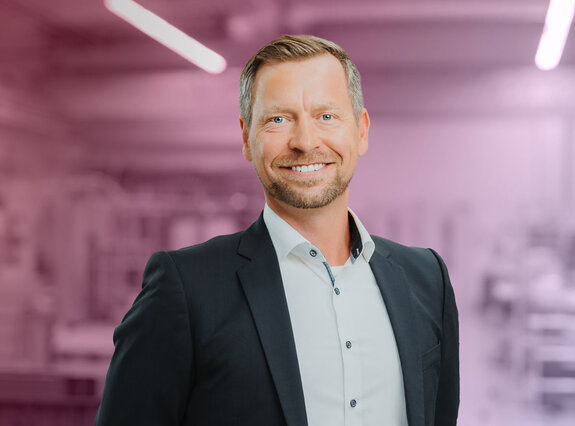
Ihr Ansprechpartner
Sie haben Fragen?
Sie wollen mehr zu unseren Projekten und individuellen Einsatzmöglichkeiten wissen? Unser Experte Peter Stiewe hilft Ihnen gerne weiter. Melden Sie sich bei uns.