Dünnschichtsensoren Inline
Hochproduktive Sputteranlage zur Herstellung von Sensoren
APPLIKATION
Selbstfahrende Autos werden Realität, Smartphones verwandeln Laien in Messgeräteexperten und Hobby-Tüftler erschaffen mit Mini-Computern automatisierte Systeme für Zimmerpflanzen. Heutzutage ist komplexe Automatisierung kostengünstig und allgegenwärtig. Dafür unverzichtbar: eine Vielzahl an Sensoren. Sie erfassen Daten wie Temperatur, Abstand, Druck, Kraft, Luftfeuchte, pH-Wert, Gas-Konzentration und mehr, um aus theoretischen Simulationen praktische Alltagshelfer zu machen.
ANFORDERUNGEN AN DIE ANLAGE
Mit der Anlage sollen Sensoren produziert werden, d. h. Leiterbahnen, Kondensatoren und Widerstände. Dafür sind auf 100 mm x 100 mm großen Wafern vollflächig dünne Metallschichten abzuscheiden – die Strukturierung per Laser oder Lithographie wird vom Kunden außerhalb der Anlage durchgeführt. Je nach Sensor sollte die Schichtdickenabweichung bei weniger als +/- 5% bzw. weniger als +/- 10% liegen. Statt Einzelschichten müssen auch Stapel aus bis zu zwei verschiedenen Metallen nach vorher definierten Rezepten abgeschieden werden. In jedem Falle ist aber eine gute Haftung auf dem Untergrund erforderlich. Von diesen Wafern müssen pro Arbeitstag 100 bis 200 Stück beschichtet werden; in Einzelfällen sogar beidseitig. Da zukünftige Sensorprodukte möglicherweise mehr Materialien benötigen, wäre eine Erweiterbarkeit der Anlage für die Zukunft wünschenswert.
LÖSUNG DER ANFORDERUNGEN
Die FHR.Line.700-V ist eine kompakte Inline-Anlage, bei der der Substratträger aufrecht stehend durch die Anlage fährt. Die Ein- und Ausgabe der 12 bis 16 gleichzeitig zu beschichtenden Wafern erfolgt über dieselbe Schleusenkammer. Die Schleusenkammer ist rund und mit einer Wendevorrichtung für den Substratträger ausgestattet, sodass die Wafer auch von der Rückseite beschichtet werden können. Die durchgängig evakuierte Prozesskammer beinhaltet eine Ätzeinheit zur Vorreinigung und Aktivierung der Substratoberfläche (für bessere Haftung) sowie zwei planare DC-Sputterquellen zur Metallabscheidung. Der Substrathalter fährt gemäß aktivem Rezept in definierter Geschwindigkeit und Häufigkeit an diesen Prozessstationen vorbei. Für einen komfortablen Zugang bei Wartungen befinden sich die Prozesseinheiten an großen Türen. Am Ende der Prozesskammer befindet sich ein großer Blindflansch, an den bei Bedarf weitere Prozesskammern nachgerüstet werden können. Wie bei allen FHR-Anlagen wird auch hier per Rezept alles automatisiert gesteuert. Alle Daten werden zur späteren Nachvollziehbarkeit aufgezeichnet.
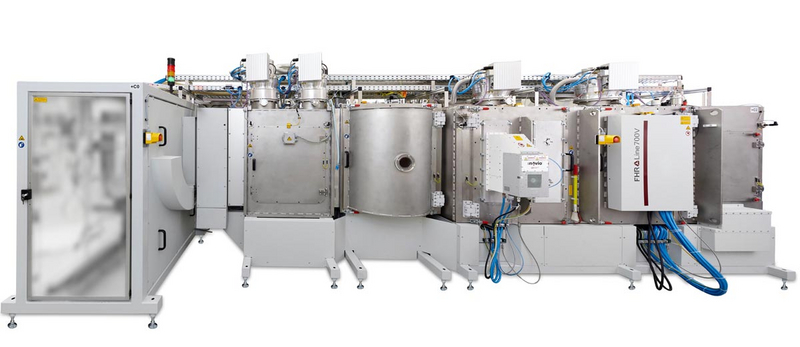
DIE BESONDERHEITEN DER FHR.Line.700-V
- Hohe Produktivität dank Beschichtungsfläche von bis zu 500 mm x 500 mm
- Kompakt dank kleiner Stellfläche der Anlage selbst von nur 0,9 m x 3,3 m
- Beidseitige Beschichtung möglich
- Automatisierte Beschichtung mit voller Kontrolle über alle Prozessparameter

Ihr Ansprechpartner
Sie haben Fragen?
Sie wollen mehr zur FHR.Line-Produktreihe wissen? Unser Experte Sven Häberlein hilft Ihnen gerne weiter. Melden Sie sich bei uns.