Thin Film Sensors – Inline
Highly productive sputtering system for the production of sensors
APPLICATION
Self-driving cars are becoming a reality, smartphones are transforming amateurs into measuring device experts, and hobby inventors are using mini-computers to create automated systems for houseplants. Nowadays, complex automation is inexpensive and ubiquitous. And an indispensable element for this is: a large number of sensors. They record data such as temperature, distance, pressure, force, humidity, pH value, gas concentration and more, in order to turn theoretical simulations into practical everyday helpers. The market for low-cost sensors is growing. As a result, more and more sensor manufacturers are asking themselves how they can make sensors cheaper and smaller. The answer is: thin film technology.
REQUIREMENTS FOR THE SYSTEM
The system will be used to produce sensors, i.e. conductors, capacitors and resistors. For this purpose, thin metal layers must be deposited over the entire surface of 100 mm x 100 mm wafers – structuring by laser or lithography is carried out by the customer outside the system. Depending on the sensor, the layer thickness deviation should be less than +/- 5 % or less than +/- 10 %. Instead of individual layers, stacks of up to two different metals must also be deposited according to previously defined formulas. In any case, good adhesion to the substrate is required. Between 100 and 200 of these wafers have to be coated per working day; in some cases even on both sides. As future sensor products may require more materials, it would be desirable for the system to be expandable in the future.
SOLVING THE REQUIREMENTS
FHR.Line.700-V is a compact inline system in which the substrate carrier moves through the system in an upright position. The 12 to 16 wafers to be coated simultaneously are fed in and out via the same lock chamber. The lock chamber is round and equipped with a turning device for the substrate carrier so that the wafers can also be coated from the back. The fully evacuated process chamber contains an etching unit for pre-cleaning and activation of the substrate surface (for better adhesion), as well as two planar DC sputter sources for metal deposition. The substrate holder moves past these process stations at a defined speed and frequency in accordance with the active formula. The process units are located on large doors for easy access during maintenance. At the end of the process chamber, there is a large blind flange to which further process chambers can be retrofitted if required. As with all FHR systems, everything is controlled automatically by formula. All data is recorded for subsequent traceability.
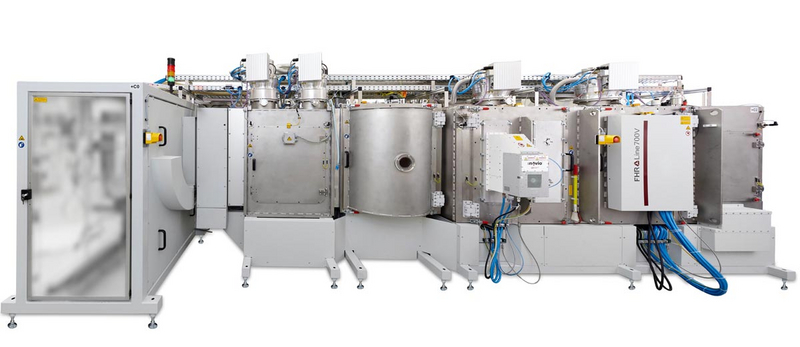
THE SPECIAL FEATURES OF THE FHR.Line.700-V
- High productivity thanks to coating area of up to 500 mm x 500 mm
- Compact thanks to the small-scale footprint of the system itself of just 0.9 m x 3.3 m
- Coating possible on both sides
- Automated coating with full control over all process parameters

Your Contact Person
Do you have any questions?
Would you like to know more about FHR.Line product range? Our expert, Sven Häberlein, will be happy to help you. Get in touch with us.