Optical coatings with different properties
Optical coatings are often used to increase (mirror) or reduce (anti-reflective) the reflective properties of a surface. They can also be used as optical filters to change the reflection depending on the wavelength. We essentially distinguish between two types: those with metal coatings and those with dielectric coatings.
Find out more about the possibilities of optical coatings.
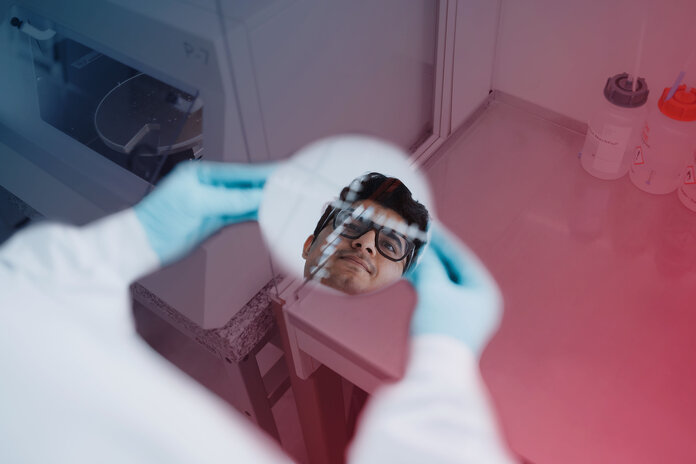
What We Offer
HIGHLY REFLECTIVE (HR) METAL COATINGS
The reflectivity of metal coatings is essentially determined by the optical properties of the metals themselves. Examples of optical metals include aluminum, chrome, gold, copper, or titanium.
Uniformly high reflectivity in the UV, VIS, and IR range
- Aluminium (Al)
Highest reflectivity in the VIS range
- Silver (Ag)
Highest reflectivity in the IR range
- Gold (Au)
- Copper (Cu)
The unique properties of metals are suitable for special coatings. An approximately 50 nm thin gold coating is partially transparent in visible light and highly reflective in the IR range. This makes them ideal for coating heat protection visors or welding protection glasses.
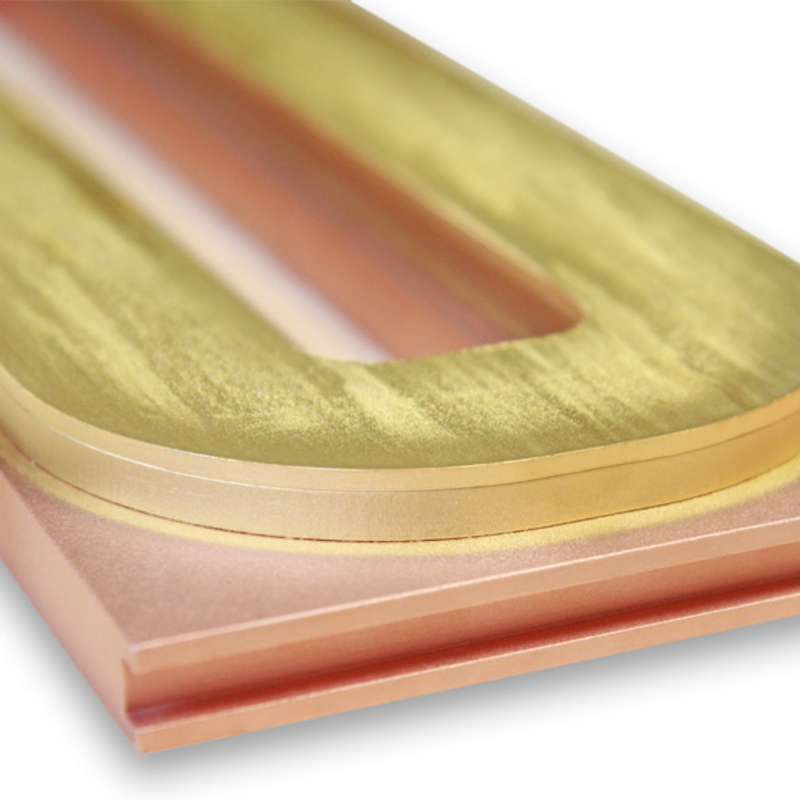
Anti-reflective (AR) dielectric coatings
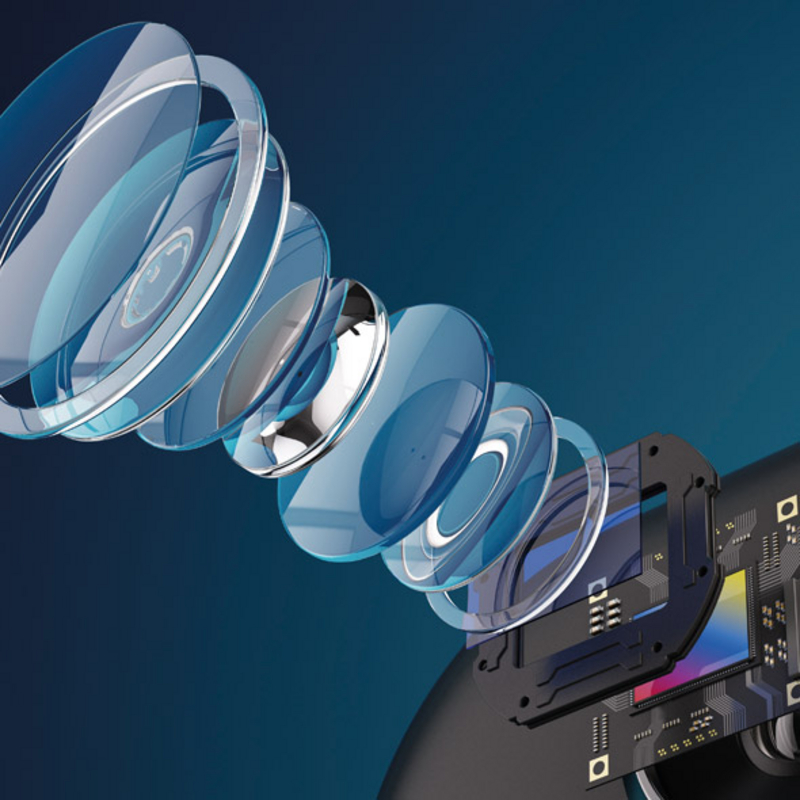
The reduction of reflection on glass surfaces can be achieved by applying a so-called λ/4 coating – such as magnesium fluoride (MgF2). If the coating thickness d is selected so that d = λ/(4 x n) - where n is the refractive index of the material – the reflected light waves of wavelength λ are canceled out at the two interfaces (air/coating and coating/glass) by superposition. The result is reduced reflection.
An alternative method uses triple coatings, whereby the refractive indices are selected so that they lie between air and glass. The anti-reflective effect is achieved here by carefully selected refractive indices that create a gradual transition from the refractive index of the air to that of the glass.
The use of multi-coating systems is recommended for demanding optical coatings that minimize reflections and increase light transmission. Such multiple coatings consist of material coatings with different refractive indices in precise thicknesses. The numerous interfaces and the associated reflections in the system lead to superimpositions – both destructive and constructive – and influence optical behavior.
Uniformly high reflectivity in the UV, VIS, and IR range
- Magnesium fluorite (MgF2) with n = 1.38
- Silicon oxide (SiO2) with n = 1.46
- Aluminium oxide (Al2O3) with n = 1.67
Highest reflectivity in the VIS range
- Titanium oxide (TiO2) with n = 2.55
- Tantalum oxide (Ta2O5) with n 2.20
- Zirconium oxide (ZrO2) with n = 2.15
- Silicon nitride (Si3N4) with n = 2.05
LOOKING FOR A SPUTTER TARGET?
We develop and manufacture sputtering targets up to 4000 mm target length as required – both in large series and as individual items.
Filter coatings
Filter coatings that selectively transmit certain wavelengths utilize coating systems consisting of materials with high and low refractive indices. For complex filter applications that only allow a narrow wavelength range to pass through, the structure can consist of hundreds of individual coatings. The uniformity of the coating thicknesses is particularly important in this regard. Further information can be found on our FHR.Star-EOSS® page.
FHR Anlagenbau GmbH utilizes special techniques to apply these dielectric coatings – including medium-frequency sputtering (MF), high-frequency sputtering (HF), pulsed DC sputtering, and reactive sputtering.

FHR – The Right Partner at Your Side
Shaping the future together – with reliable and high-quality coating solutions from FHR:
- Industry-leading quality: Our vacuum coating systems are designed for maximum precision and durability.
- Customized solutions: We offer individual solutions for your coating project that meet your specific requirements.
- Innovative methods and technologies: With our many years of experience and expertise in vacuum coating, we continue to set new standards.
- Dedicated customer service: Our experienced team is always available to answer your questions and provide you with support in your projects.
Discover the diverse range of possibilities with our vacuum coating technology, and place your trust in FHR as your reliable partner for outstanding coating solutions. Please feel free to get in touch with us to find out more and realize your projects together.
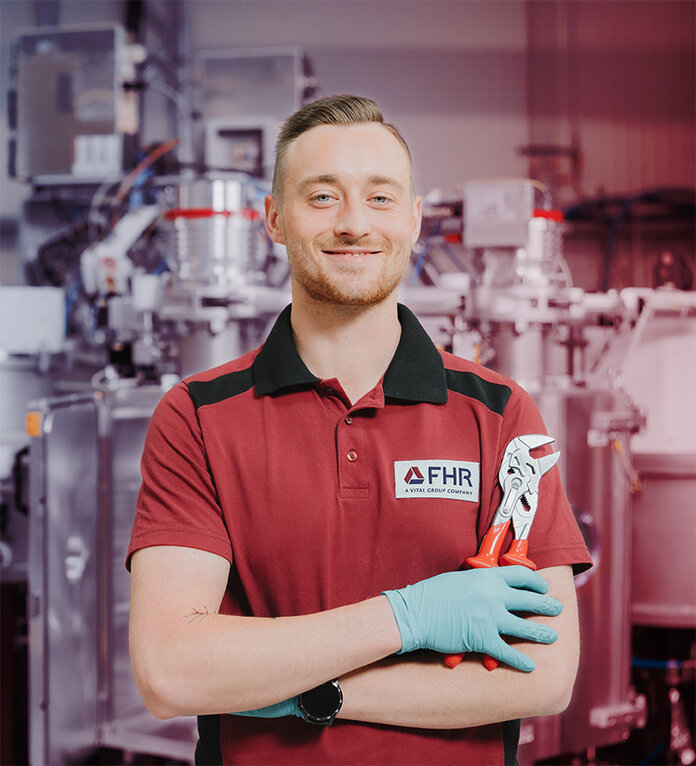
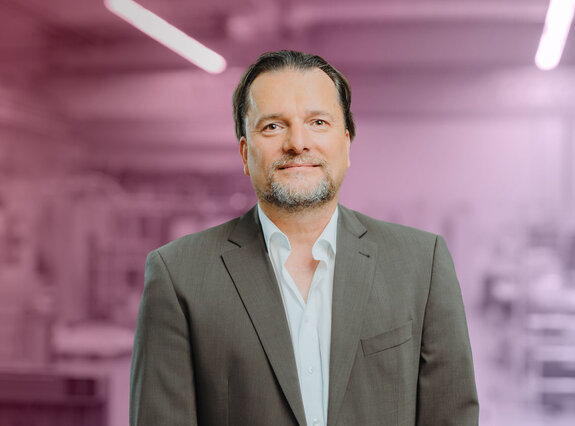
Your Contact Person
Do you have any questions?
Would you like to know more about optics and coatings? Our expert team will be happy to help you. Get in touch with us.