Precision Optical Filters
Precision sputter coating system for interference optics applications
APPLICATION
Numerous modern measurement methods and large parts of telecommunications are based on optical processes.
Optical filters must remove individual wavelengths from the light beam (notch filters), only allow defined wavelengths to pass through (bandpass filters) or switch from reflection to transmission from a certain wavelength (edge filters).
Interference-optical stacks of thin dielectric layers, which alternate between high and low refraction, serve as optical filters.
REQUIREMENTS FOR THE SYSTEM
The system will be used to produce optical filters on flat substrates with a diameter of up to 200 mm. As precision filters, they should have a particularly reproducible transmission spectrum with particularly steep edges and particularly low scattering. That means technologically: Stacks of 50, 100 or more layers must be deposited, whereby the thicknesses of each individual layer must be precisely adhered to (and deposited over) the entire substrate with a deviation of less than +/- 1 %. Optically relevant particles should be avoided. Another requirement: the system must process formulas fully automatically and achieve a high throughput.
SOLVING THE REQUIREMENTS
FHR.Star.500-EOSS® represents a further development of the Enhanced Optical Sputtering System (EOSS®) conceptualized jointly with the Fraunhofer Institute for Surface Engineering and Thin Films. It is the most advanced product currently available on the market for the production of interference optical filters.
SPECIAL FEATURES OF FHR.STAR.500-EOSS®
- Outstanding reproducibility
- Extremely low particle count thanks to sputter-up process
- Optimal layer growth through bipolar controlled double sources
- Highest material utilization and longest target service life through the use of tubular cathodes
- Best coating quality thanks to broadband monitoring and in-situ error compensation using MOCCA+®
- A design uncompromisingly geared towards production processes
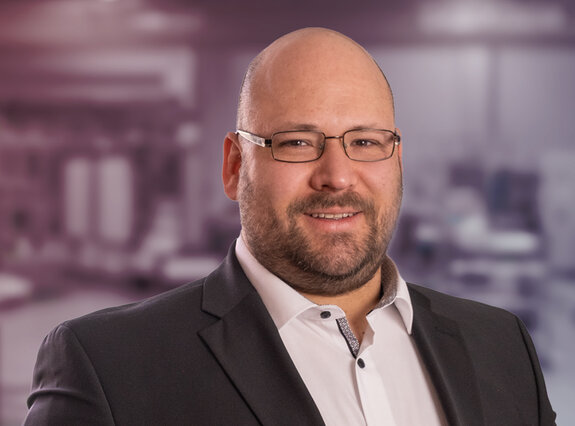
Your Contact Person
Do you have any questions?
Would you like to know more about optics and coatings? Our expert team will be happy to help you. Get in touch with us.