A PROCESS FOR THE PRECISE DEPOSITION OF THIN FILMS
Physical vapor deposition, often referred to by the abbreviation “PVD”, is a process where the material is vaporized as a target in the process chamber, and applied as a thin film to the surface to be coated (substrate). Subsequently, many different materials can be deposited on a wide variety of substrates.
Find out more about vapor deposition technology.
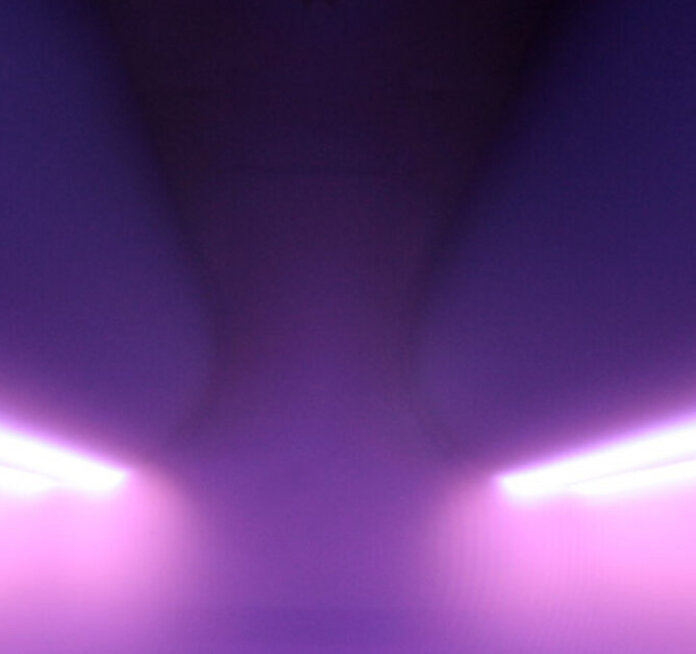
How It All Works
What is physical vapor deposition (PVD)?
Physical vapor deposition, or PVD for short, refers to techniques used to apply thin coatings to substrates. All of these processes are carried out in a vacuum.
The most frequently used and, from an economical standpoint, most important PVD process is sputtering. Due to its high flexibility, it is used in numerous industries. Sputtering can be used to apply many different materials to a wide variety of surfaces. It is used, for example, in the semiconductor industry, in the finishing of materials, in the optical industry and even in the coating of large glass surfaces on buildings. FHR Anlagenbau GmbH is a global technology leader in this segment. FHR manufactures first-class coating systems and sputtering targets of the highest quality. Our expertise in this discipline is the result of many years of experience and a passion for innovation.
In the PVD process, the material – known as the target – is kept in solid form in the system for subsequent thin film coating. This material is then vaporized, and grows as a thin film on the substrate surface. There are various methods that can be deployed when vaporizing the material, e.g. with a laser, an electric arc or by bombarding it with particles.
There are also PVD techniques in which the material is transferred into a gas state by heating (thermal vapor deposition). Molecular beam epitaxy and ion beam-guided deposition also belong to the group of PVD processes. The resulting coatings are particularly pure, uniform and achieve a very high level of adhesion to the substrate. PVD coatings, therefore, offer an environmentally friendly alternative to conventional electrochemical processes for numerous areas of application.
Physical vapor deposition offers several advantages over other thin film deposition techniques:
- High-purity coatings: As PVD takes place in a vacuum environment, the deposits typically remain unaffected by atmospheric impurities, resulting in particularly pure coatings.
- Thin and even coatings: PVD enables the production of extremely thin, uniform, and adhesive coatings that adhere well, even when involving complex surface structures.
- Versatility: Various materials – from metals to ceramics – can be deposited as thin films using PVD, which enables a wide range of applications.
- Environmental friendliness: Compared to some wet chemical processes, PVD generally does not use hazardous chemicals, minimizing environmental impact and waste.
- Long service life of coatings: PVD coatings are often hard and corrosion-resistant, which can extend the service life of tools and other coated objects.
- Economic efficiency: Despite the initial cost involved with PVD systems, the long-term benefits in terms of material yield, maintenance, and improved product life can lead to economic advantages.
These advantages make physical vapor deposition a preferred method for many industrial and scientific applications.
Vacuum coating systems
Discover how our vacuum coating systems form the basis for high-performance coatings in numerous industries, and how our technologies can be used for your projects.
FHR – The Right Partner at Your Side
Shaping the future together – with reliable and high-quality coating solutions from FHR:
- Industry-leading quality: Our vacuum coating systems are designed for maximum precision and durability.
- Customized solutions: We offer individual solutions for your coating project that meet your specific requirements.
- Innovative methods and technologies: With our many years of experience and expertise in vacuum coating, we continue to set new standards.
- Dedicated customer service: Our experienced team is always available to answer your questions and provide you with support in your projects.
Discover the diverse range of possibilities with our vacuum coating technology, and place your trust in FHR as your reliable partner for outstanding coating solutions. Please feel free to get in touch with us to find out more and realize your projects together.

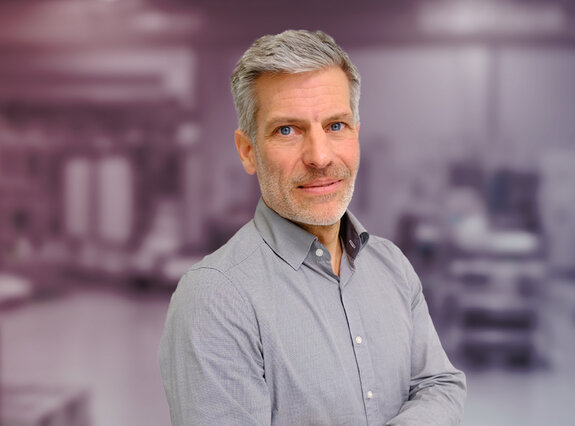
Your Contact Person
Do you have any questions?
Would you like to discover more about thin film technology or receive general advice on our vacuum coating systems and our coating service? Then feel free to get in touch with us – our team of experts will be happy to answer all your questions.